Understanding Aviation Inventory Management System
Aviation parts inventory management systems are specialized software suites and systems used by aviation operations and maintenance departments to track millions of parts globally. These powerful systems inventory the parts supplied within their organization in real time.
When we are talking about military flight operations, parts inventory management is a national security matter and cannot be taken lightly. So, when you wonder, “How do I manage my spare parts inventory?” the solution is usually an aviation parts inventory management system. But which one is best? Or is there a best one? Let’s take a look and find out.
What Are the Problems With Legacy Supply Systems?
“How do I track my stock?”
“How can I keep it updated?”
For every 100 characters, an input operator makes one error. Because you probably sell a lot more stock than you have, that can cause serious headaches. Automating processes increases efficiency, enhances accuracy, and enables business growth. Excel files can be slow and inaccurate and can't be opened by multiple computer users simultaneously. Using the Automated Inventory Manager, you can view the tracking of items at different locations while analyzing orders/shipments for each.
Excel is a powerful tool that has proven extremely valuable over the years but has strict limitations. For one thing, you need to have a good basic understanding of how it works.
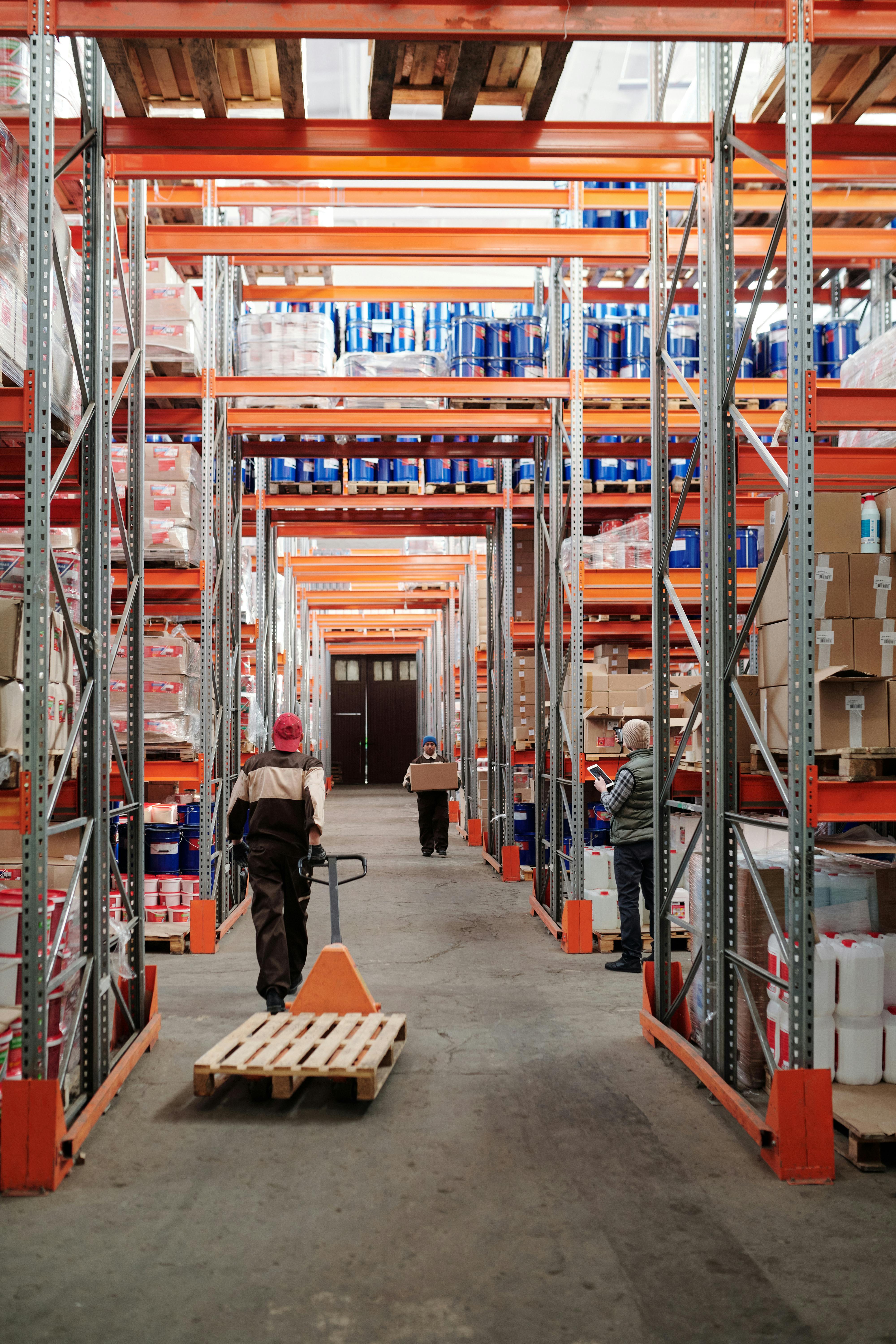
How Are Aircraft Parts Currently Inventoried
The methods used for inventorying aircraft parts vary based on the complexity of the organization, the quantity in inventory, and the level of detail needed.
Automated inventory management is a straightforward and less complicated method, but it is time-wasting and error-prone. Barcodes and RFID tags can simplify tracking and improve accuracy, but they are fairly costly to implement. Computerized inventory managers offer the most flexibility and accuracy but may even be the most expensive to implement. Of course, it is non-negotiable with a large fleet of military aircraft.
Traditionally, Part Inventory Management Relied Heavily On Manual Inputs
Aircraft inventory management is about as old a process as military aviation. There have always been warehoused spare parts for aircraft, and it is hard to imagine how a flying wing of an aircraft could maintain an accurate supply chain with only paper ledgers. Constant inventory management by hand had to be the norm, and the man-hours for the process had to be unreal. And think about it in these terms: most of the Air Force inventory was designed and built when computerization was unavailable!
As we entered the computer age, paper-based logging slowly moved along (but not entirely); certain parts of the USAF supply chain management remained exclusively paper-based well into the 2000s.
Now, by this we are talking broadly about the aircraft fleet. Digital professional inventory management systems are already in place for the tactical fleets (CAMS-FM) and GO81 for the mobility fleet (although word is that the Air Force is migrating to a single system).
However, this leaves a lot of gray areas for some aircraft that don’t fall under the military model for parts storage and procurement.
Ready To Change How Your Unit Handles Aviation Inventory Management?
The Army’s aviation model is significantly different than the Air Force’s. The National Guard is a major component of the U.S. TRANSCOM fleet with their C-12 Huron and C-26 aircraft. Every state has at least one fixed-wing aircraft assigned to the National Guard, and these are routinely stationed as a stand-alone mission.
Sometimes, they are geographically located with an AASF, but not always. Besides, the rotary wing fleet does not standardize inventory planning, parts storage, and procurement.
One of the most cost-effective stock provisioning methods for remote units like the TRANSCOM units is partnering with Greenwood Aerospace. A remote unit is likely low on space for inventory control, which is why we offer aerospace parts storage and distribution from our 42,000 sq. foot warehouse in Ponca City, Oklahoma. Our central location and easy access to I-35 allow quick and easy access for expedited order fulfillment.
Common Mistakes to Avoid in Aircraft Parts Inventory Management
The biggest mistake to avoid with aircraft parts inventory management is poor documentation, but you need to be aware of several other items.
- Lack of documentation: if your parts inventory management software fails to maintain accurate and up-to-date documentation of the inventory in real time, you will have problems. One negative effect can be aircraft remaining in non-mission capable status due to parts unavailability when they may, in fact, be available.
- Poor organization: Your aircraft parts storage and distribution model (along with the spare parts management software) needs to ensure that parts are labeled and stored correctly. Keeping them off-site in Greenwood’s warehouse is a surefire way to ensure proper organization of parts.
- Overstocking and understocking: aerospace inventory management is a delicate balance between too little and too much. We are your fixed-wing aircraft parts procurement specialists, and military aircraft parts are our specialty. Our aviation logistics systems are second to none so that you can ensure the stocking of just the right parts. And again, we will gladly warehouse and ship the parts to you to keep inventory levels at a minimum.
- Inaccurate parts forecasting: Aviation logistics will always be a major challenge because predicting failures is hard. Of course, predicting parts like rotables with standardized replacement cycles is a little easier, but that is only part of the parts forecasting equation.
This is not a conclusive list of the common mistakes in aircraft parts and spare parts inventory management. Instead, these are the ones we see often. The best thing you can do is to give us a call and talk to one of our logistics experts to see what solution is best for your organization.
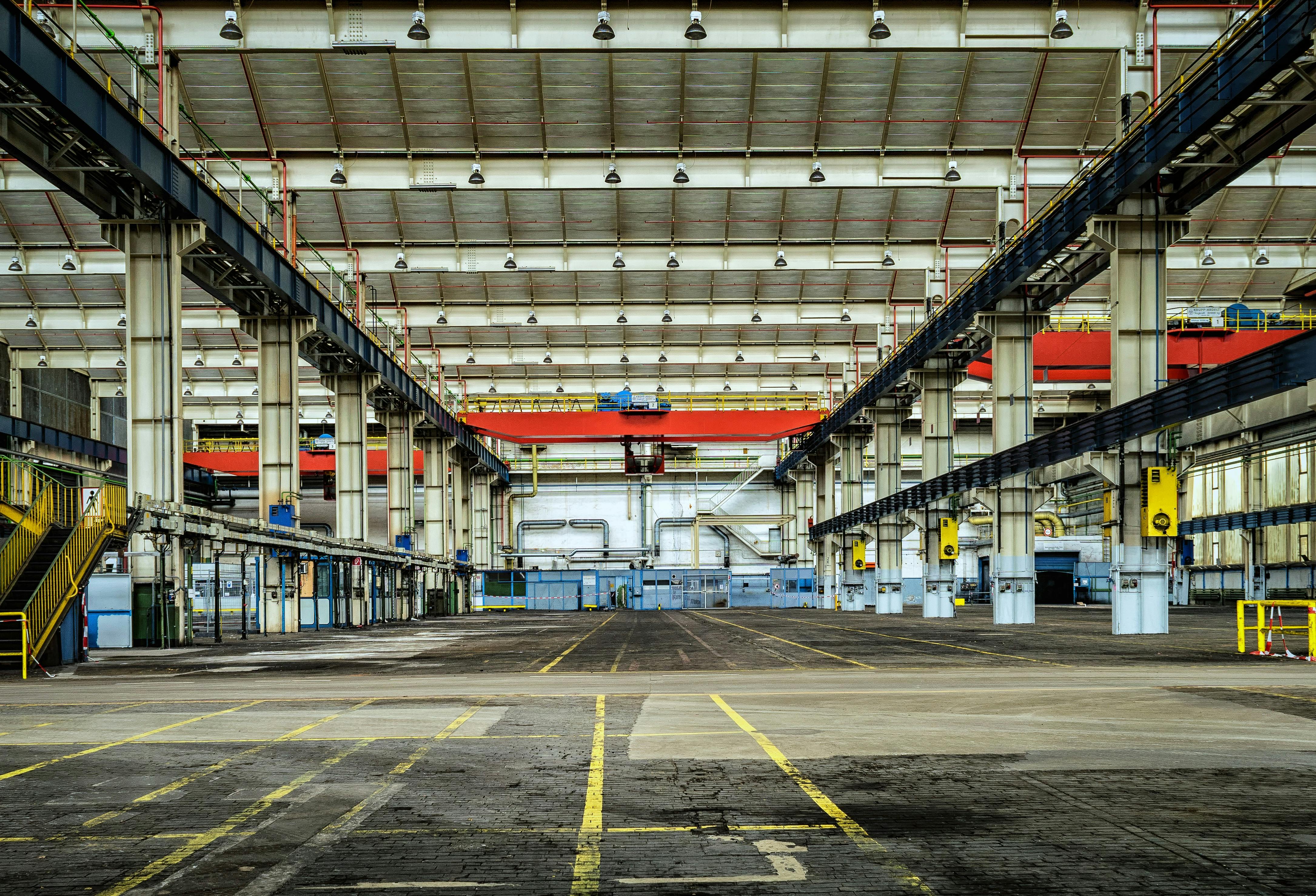
Are Spare Aircraft Parts Considered Inventory?
So, one question that comes up fairly often is whether spare aircraft parts are considered part of the inventory. The answer is yes, they are.
This is especially important for the Army fixed-wing aircraft because they usually do not have a spare aircraft on site. If they have to drop a mission because of a lack of parts, the mission gets scrubbed altogether, and the passenger has to fly commercially, or the mission falls to another unit at a location that may be less optimal for the mission profile.
So, what parts should be kept on-site when you have limited warehouse space? That really depends on your mission profile. Some of the most obvious items are:
- Tire and wheels
- Brakes
- Windscreens
- Seals for doors, windows, and hatches
- Any avionics boxes or gauges that have higher than usual failure rates
- Common powerplant parts for repairs that don’t require the removal of the engine from the aircraft
- Any other common expendable parts
Considering the missions of military aircraft, including the TRANSCOM fleet, are national security issues, contingency planning of aircraft parts is important. A contingency stock of spare parts needs to be on hand, and our procurement specialists are the best in the business.
Parting Thoughts
Aviation inventory management systems have come a long way over the years, and when organizations start using Blockchain technology, it will change even more. Greenwood Aerospace is proud to lead the charge with our GPIQ software, which ultimately sets your organization up for success by helping you partner up with the most reputable parts suppliers in the business.
Our GPIQ software focuses on market intelligence and value enhancement linked to such aircraft and was created with prime contractors that support special mission aircraft in mind. We know that maintaining the aircraft in the air is essential to any government program's success.
You get what you want, and we make it happen by adjusting GPIQ to fit your changing demands. GPIQ ensures that suppliers have undertaken stringent onboarding and qualification tests, providing important information about their prior performance.
We have over forty years of experience and have formed partnerships with the best, and we pass that along to you.