OEM Vs. MRO in Aviation
There are thousands of maintenance, repair, and overhaul stations, facilities, and companies nationwide. Some are huge sprawling operations that service fleets of airlines; others are niche performers specializing in specific systems and sub-systems. MROs are independent agents and agencies that operate on entire aircraft or specific systems with the approval of the original equipment manufacturer (OEM). This practice has gone on for decades and has proven to be a productive model for commercial operators to follow. But the OEMs are starting to return to the table as aftermarket service providers for the airline fleets.
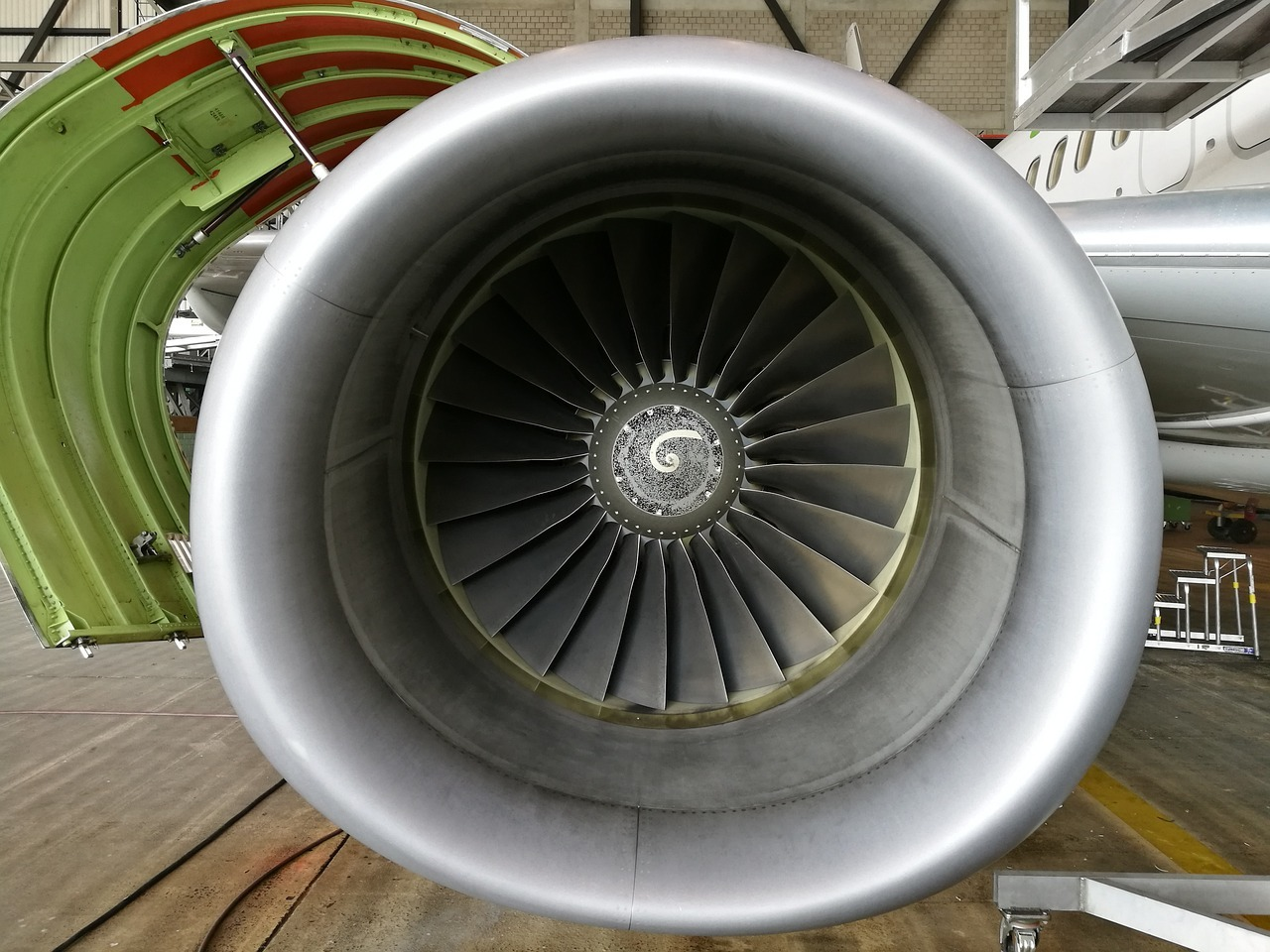
But what is the difference even? Are they the same thing or something else? And does the OEM hold specific rights to the aircraft design that MRO cannot gain authorization to? Let’s tackle these questions and more.
OEM in Aviation
The original equipment manufacturer is just that: they are the original designer and manufacturer of the aircraft. In decades past, the OEMs largely stayed out of the MRO game. Maintenance, repairs, and overhauls were handled (with a few exceptions) predominantly by aftermarket independent and airline-affiliated shops. The OEMs primarily concerned themselves with R&D for improving designs and creating new products. But the OEMs were missing out on a significant pool of revenue, OEMs have widely been reestablishing themselves in the maintenance process.
It should be stated that OEMs enjoy a significant advantage over MROs because they own the rights to:
- The intellectual property of the design
- Design data
- Manuals and schematics
Since they own all of these, OEMs can effectively control the maintenance narrative if they want to. So, MROs have decided to lean into it instead of fighting OEMs. A partnership makes much more sense instead of waging warfare with the original owner of the designs.
MRO in Aviation
Maintenance repair shops have traditionally been the movers and shakers of aircraft maintenance. The airlines owned some of the biggest shops in the world; in fact, the American Airlines maintenance center in Tulsa is the largest aircraft repair shop in the world. But repair centers are extremely expensive to own and operate, and airlines want to trim the fat wherever they can. Maintenance is one of the highest expenses of any aircraft operation, so it is generally one of the first areas to target. Some estimates are around 11% of the total operating costs of an airline go immediately into maintenance costs. Outsourcing MRO work is one strategy that can help reduce overall costs, and the airlines are exploring all options, including OEMs.
Maintenance
We need to discuss the distinctions in the nomenclature because there are distinctions between each maintenance, repair, and overhaul. Maintenance is simply that: it is the act of maintaining a piece of machinery. Line maintenance is a prime example, where systems are serviced routinely.
Examples of maintenance are:
- Hydraulic system servicing
- Engine and APU serving
- Tires
- Struts
Aircraft are inspected on set series of intervals, generally between flights, after flights, and pre-flights. All of the structures are inspected for damage (bird strikes, storm damage, lightning strikes, etc.).
Maintenance also includes minor and intermediate repairs or parts replacement which can include any number of parts on the engines, hydraulic component replacements, and avionics repairs.
Repair
Repair is a higher level than maintenance. Maintenance is generally tied to aircraft inspection as they are in between flights. Repairs are procedures that take considerably more time and will take the aircraft out of commission for an extended (but not long-term) period.
Repairs could be
- Swapping out an engine (it is often easier and more cost-effective to pull off a malfunctioning engine and replace it with a spare unit)
- Removing and replacing an auxiliary power unit
- Removing and replacing propellors
- Fixes on major assemblies, whether structural or systems (i.e., a fleetwide hydraulic system repair driven by Airworthiness Directives)
- Major corrosion repairs
- Fuselage or skin repairs
Overhaul
Overhaul is the highest level in the overall maintenance concept. This can put an aircraft or major component out of commission for weeks or even months. In the military, this is considered a ‘depot level’ process. Depot takes aircraft and strips away thousands of components for extensive repair and inspection.
Engines, APUs, and major systems components like generators, hydraulic actuators, brakes, and so on undergo overhauls. A complete overhaul of a large jet engine can easily cost over one million dollars; a CFM-56 overhaul runs about $1.1M-$1.2M and is a smaller commercial airliner engine.
The Difference
Where the rubber meets the road in aircraft maintenance, which is the tasks performed or the overhauls conducted, there is not a lot of difference between OEMs and MROs. They conduct maintenance, repair, or overhauls on aircraft and aircraft components. The big difference is in who conducts the work.
Now, here’s the thing: OEMs are looking to cash in on maintenance and repair work, which they are poised well to do due to their ownership of all rights to the design. But the OEMs also have some serious hurdles to overcome before they can topple major MROs in the airline maintenance game.
Benefits of OEM
The OEMs do have some real advantages, to be sure, but they have a long way to go before they mop up the MRO segment.
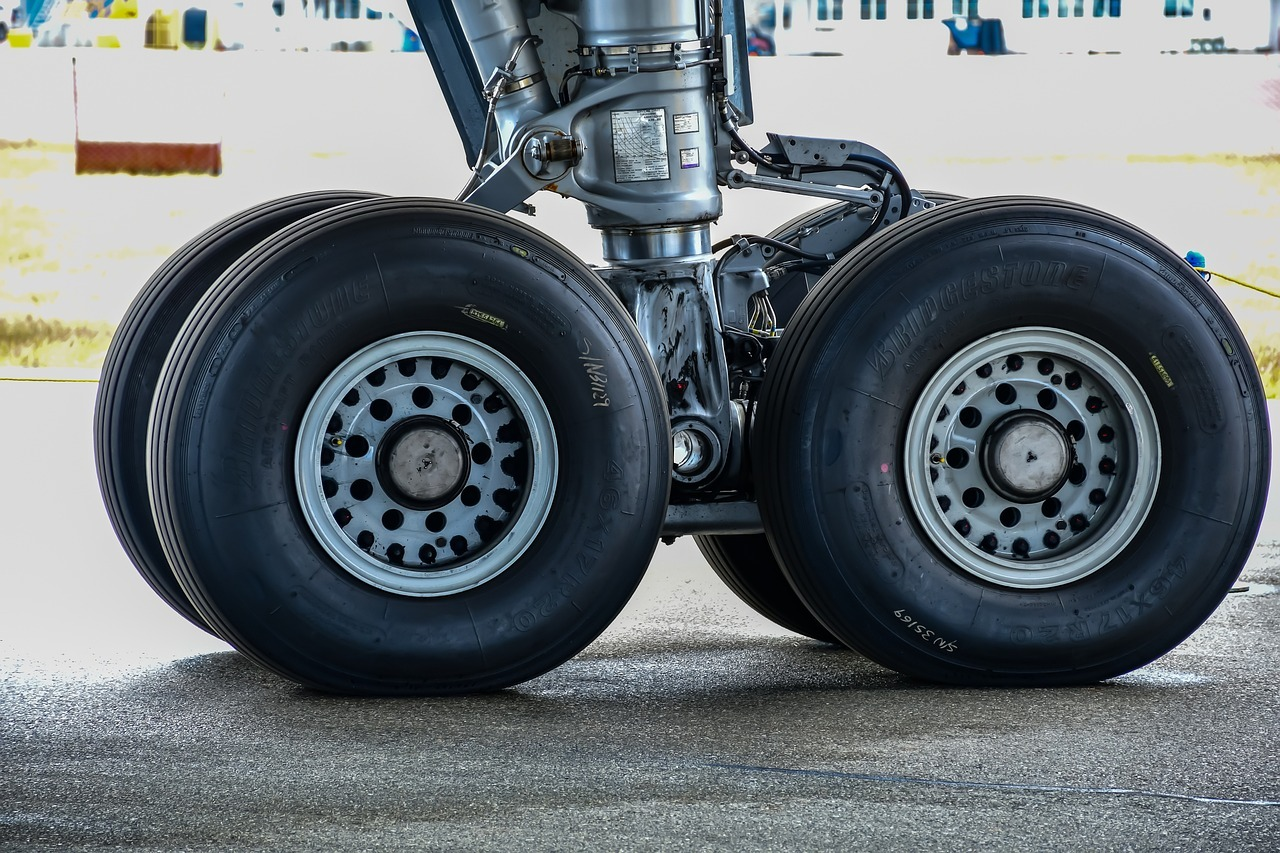
Quality of Parts
The quality of parts is a huge concern. Inferior parts quality is always a major concern with repairs, especially with the scourge of rampant non-certified parts from overseas being a constant concern. An OEM develops and produces their own parts, which they produce during production. They own the dies, they own the technical specifications, and they own the drawings.
Reduced Development Time
Since OEMs own all of the rights to the designs and they have all of the original engineering paperwork, drawings, diagrams, etc., the development time will be faster.
The design rights are a huge advantage. They don’t have to ask permission to modify the design, which can save them months during the process.
Specialized Expertise
OEMs benefit from being the ultimate subject matter experts in designing parts for their original aircraft or aircraft components.
Benefits of MRO
MROs are not out of the fight by a mile. They still offer huge advantages that will be hard for OEMs to overcome, which makes partnerships a much better compromise.
Flexibility
OEMs are actually limited in what they can service because they can only service their OEM designs. An MRO can easily pivot. What does this mean?
Say an airline starts with Boeing 737s only. Boeing could be the OEM to service them. But then the airline incorporates Airbus A330s into the fleet, for instance. An MRO can easily pivot to accommodate both airframes.
The same principle applies to MRO for major components. An engine MRO that repairs CFM-56s can easily pivot to other engines and probably does anyway to begging with. Also, OEMs will have decades of experience and relationships that MROs have forged with major airlines to compete with.
Efficiency
MROs have spent years ironing out the wrinkles of inefficiency, especially when working with airlines. Airlines are in a constant state of growth, and their demands and performance expectations of maintenance grow. MROs have proven capable of growing and increasing capacity as needed; OEMs will probably struggle with this because they aren’t designed for it. They are built around manufacturing principles, which are not the same thing.
Cost-Effectiveness
The airlines are always swaying, pivoting to wherever the market directs them. MROs represent a more reliable model to adjust with the airlines, who don’t want to be locked into contracts that will be full-service by an OEM. Airlines want the freedom to select what they want instead of ‘select-all.’ MROs offer that.
The Rise of OEMs in the MRO Sector
OEMs will not miss out on all that revenue that has been going to airline-owned or private MROs for years, but they have much catching up to do.
For one, private MROs have been making inroads with the airline's maintenance for decades, and OEMs will have to do the same. They must prove that they can provide the same level of service as an MRO at a comparable price point. But they still will not have the flexibility to service other OEMs, which could be a long-term problem.
Conclusion
OEMs will continue to gain traction, but it will probably be slow. MROs are profoundly entrenched and incredibly experienced. They also hold enormous amounts of data on aircraft maintenance from the fleets, which is far different than design and manufacture. In this regard, the MROs really hold the keys to the kingdom. The OEMs, though, will likely trump them in parts procurement because they can and do produce their own OEM parts, whereas MROs must source them.
What we will most likely see are further alliances between OEMs and MROs, so that they can work symbiotically rather than at odds with each other. OEMs don’t have the track record of MROs, but MROs are hampered in parts production and procurement. Collaboration makes the most sense.